What is Lean?
Lean is the same as Lean manufacturing or Lean production. Indeed, it is a method elaborated based on the Toyota Production System back in the 30s, renamed today the Toyota way. Sometimes, it is known as LSS, Lean-Six Sigma when Lean is bundled with the 6 Sigma (6σ) approach. As a matter of fact, quality target in 6 Sigma (6σ) is to reach the 5 nine quality (99.99966%% perfect).
In addition, Lean also applies to services as Lean Services but the principles and practices are the same.
- What is Lean?
- How to implement Lean? Let's review more in detail, principles and practices
- What’s next? Learn more about Agile and its two main frameworks, Scrum, Kanban and the differences between Agile and Lean
- Do you want to learn more about Lean and the Toyota Production System? Here are some valuable references
The Toyota way: principles and practices in the House of Lean

Today, the Toyota way consists in 2 pillars, the values Respect People and Continuous Improvement, and 5 principles as listed below:
– Challenge: We form a long-term vision, meeting challenges with courage and creativity to realize our dreams.
– Kaizen: We improve our business operations continuously, always deriving innovation and evolution.
– Genchi Genbustu / Go and see: We practice Genchi Genbutsu (onsite hands-on experience), go to the source to find the facts to make correct decisions, build consensus and achieve goals at out best speed.
– Respect: We respect others, make every effort to understand each other, take responsibility and do our best to build mutual trust.
– Teamwork: We stimulate personal and professional growth, share the opportunities of development and maximize individual and team performance.
Moreover, Lean is especially famous for its wastes, Mudas in Japanese. Taiichi Ohno, a past Toyota executive, invented them. Here are the 8 Mudas or wastes:
- Defects,
- Over-production (produce more than expected by the customer),
- Waiting,
- Non-utilized talent (added later the creation of Mudas by Taiichi Ohno),
- Transportation unnecessary of materials, product, equipment or tools,
- Inventory,
- Motion of people,
- Extra-processing (doing more work than needed to complete a task).
Lean Manufacturing: overview on principles and practices
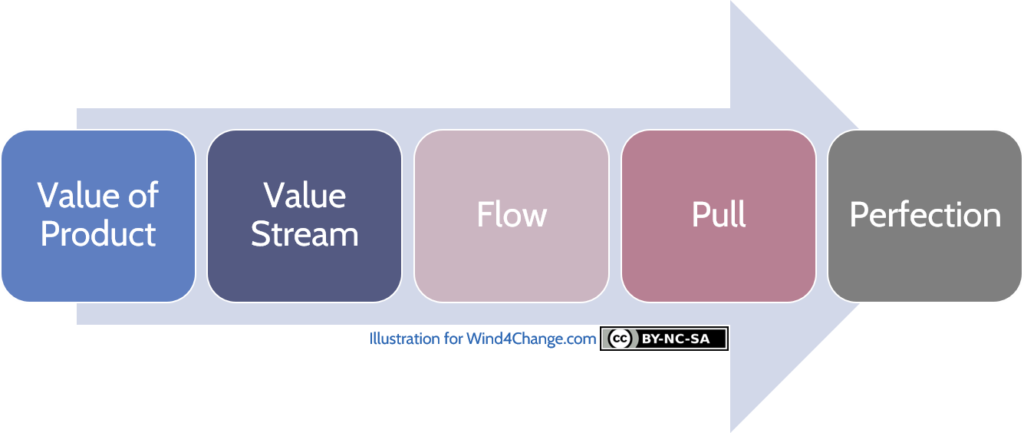
John Krafcik invented in 1988 the expression “Lean”. Then, searchers James Womack and Daniel Jones described Lean or Lean Manufacturing in 1996 over 5 principles that can also seen as the 5 steps to implement it:
Precisely specify value by specific product, identify the value stream for each product, make value flow without interruptions, let customer pull value from the producer, and pursue perfection.
How to implement Lean? Let’s review more in detail, principles and practices
Value
All start with precisely identifying the value expected by the ultimate customer through a dialogue. This value is expressed as features of the product, the service or a combination of both, to meet the customer’s needs for a specific price at a specific time.
Value Stream
The Value Stream is the collection of all the activities required to design, build and deliver the product or service to the customer. Some activities create value in the end product or service. Furthermore, some others do not, but are mandatory (type 1 Muda, aka waste). At last, some activities do not create value and can be avoided (type 2 Muda).
Flow
Flow is the alignment of all the means either people, equipment, tools or materials on the Value Stream. Indeed, this is a move away from function, department silos and from batch and inventory. Truly, the target is a continuous processing or at least a drastic reduction of the size of inventory and batch.
Taiichi Ohno blamed this batch-and-queue mode of thinking on civilization’s first farmers, who he claimed lost the one-thing-at-a-time wisdom of the hunter as they became obsessed with batches (the once-a-year harvest) and inventories (the grain depository).
But flow thinking is counter-intuitive, as Taiichi Ohno reminded with is image about common sens from farming. Most people think that organizing by department and delivering batches is the obvious way to be efficient. Actually, this organization by department is self-maintaining because career paths connect to and protect departments and because corporate accounting focuses on maximizing use of assets.
Nevertheless, the alternative approach coming with Lean is to stream-line the work of functions and departments. Really, this allows moving from local level optimization to value stream level optimization. So it becomes possible to optimize globally all contributions to create value and to meet customer’s expectations. In addition, this can go outside the company and involve partners to deliver the product or service to the customer.
Once the Value Stream is defined and all means are aligned on it, then activities are reviewed for waste hunting and optimization. First round of optimization is a radical improvement, Kaikaku. Following rounds switches to continuous improvement, Kaizen.
Pull
Pull in Lean is the idea of building the product or service when requested by the customer. Not in advance. Obviously this is only possible by reducing the total time to build or deliver the service and by reducing the unitary cost so big batch producing is not required any longer. All this comes with the Lean implementation activities described above and allowing more optimization with Pull. Another side effect of reducing batch and inventory is to reduce unsold product that end out discounted or even worse disposed.
Kanban comes from Japanese and, as the term means, it is a signboard or billboard. It is a famous Lean tool to visual the flow and pull production from the demand. It supports Just in Time that is production when needed, when requested by the customer.
Perfection
The last step is never ending as continuous improvement keeps going with perfection as target.
There is no end to the process of reducing effort, time, space, cost, and mistakes while offering a product which is ever more nearly what the customer actually wants.
Definitively, total transparency supports closely Continuous Improvement. When there are all stakeholders in the system, contractors and first-tier suppliers included, it is easier to discover new ways to optimize or to create more value to the customer.
What’s next? Learn more about Agile and its two main frameworks, Scrum, Kanban and the differences between Agile and Lean
- Read more about Agile.
- Discover the differences between Lean and Agile.
- Check the two main Agile frameworks and review my posts on Scrum and Kanban.
- Get an introduction to Agile at Scale.
- There are also plenty of other materials around Agile and Agile at Scale.
Do you want to learn more about Lean and the Toyota Production System? Here are some valuable references
Some valuable books
- Lean Thinking, the book from James Womack and Daniel Jones, quoted several times in this post
- The Machine that Change the World, another book from James Womack and Daniel Jones on the topic